Primary Engineering Systems
Construction
Vornado/Charles E. Smith Commercial Realty, the owner, entered into preconstruction services with Balfour Beatty Construction, the general contractor, for Crystal Plaza II in August 2006. Crystal Plaza II is a renovation/addition of an existing, 205,000 square foot, commercial structure located on 20th Street, Alexandria VA, within the area known as Crystal City, into a 325,000 square foot residential, multi-family complex.
The contract for Crystal Plaza II is a negotiated contract with preconstruction services provided by Balfour Beatty and delivered as a guaranteed maximum price of $67.3 million. Crystal Plaza II presents the general contractor with many challenges, including the unknowns associated with renovation of an existing building and its attempt to achieve LEED silver. Primary concerns are with the structural system given its original design and the numerous amount of penetrations that must be added to support the residential systems for the new building use. Another concern is the installation of the curtain wall system while the upper floor slabs are being placed. Because the lower floors are already complete, installation of the curtain wall system can begin immediately, however, additional protection and precautions must be used to ensure that the custom built curtain wall is not damaged. This is accomplished by using a protective “brow” system that surrounds the structure at a given level.
The general contractor has supplied a two car, man/material hoist on the south side of the building that starts at the 2nd floor and includes a single jump from the initial height at the 12th floor to the final, 20th floor. Also provided is a Peiner Model SK225 tower crane with a 268’ hook height and a 163’ boom length. The crane is just high enough to place the cooling tower units alongside the penthouse on the 20th floor. The crane’s primary use on site is for the concrete subcontractor, but is available to other trades until its removal in mid September.
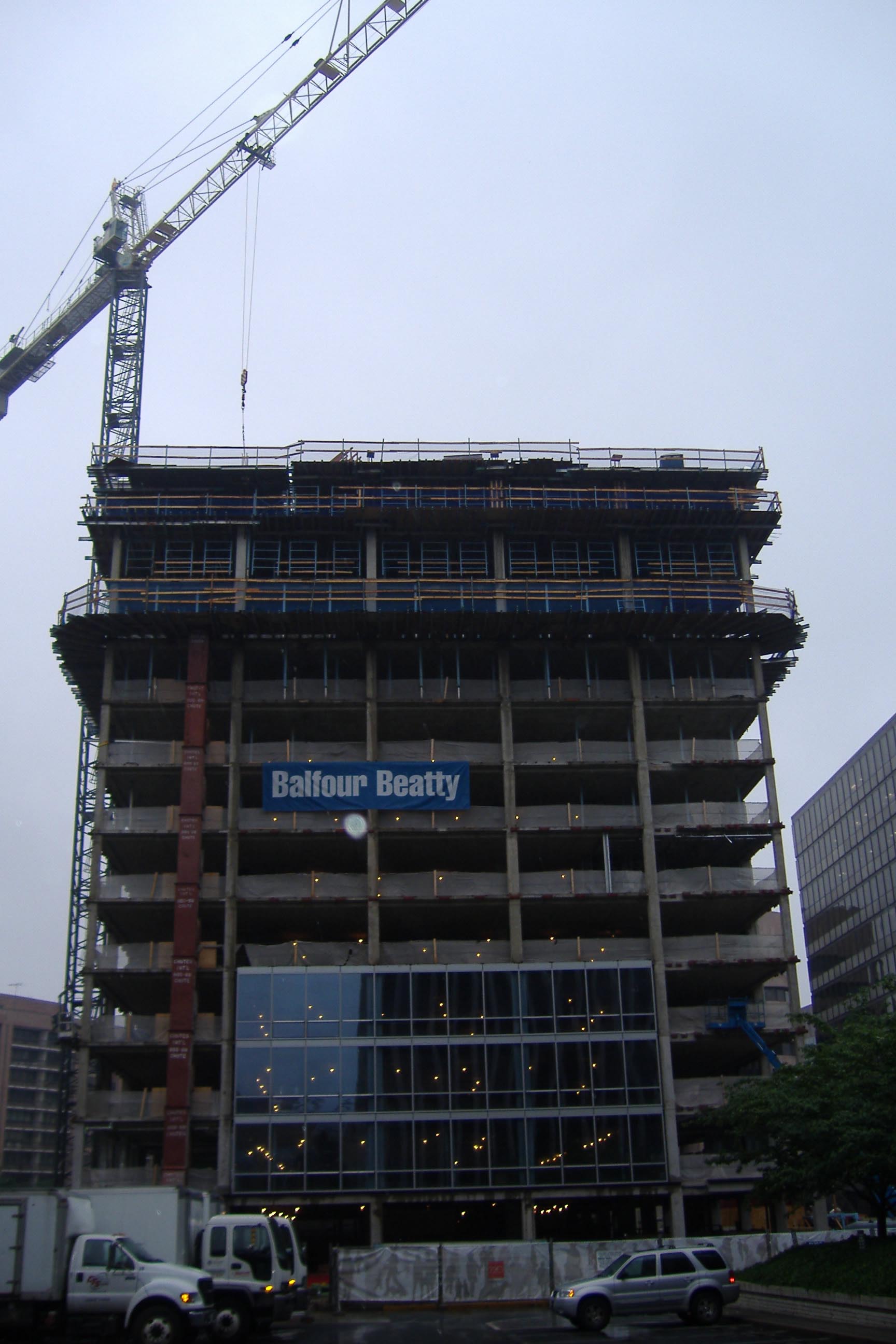
Electrical
Apartment units will receive 120/208 V, 125 A service via 19 meter centers located on each floor in the electrical closet. Meter centers are broken into two supplies, one from floors 2-10 and a second for floors 11-19. Meter centers are connected to a single, 3 phase, 5000 A switchboard by bus duct with a primary riser size of 2500 A and connection ducts of 600 A that is part of Dominion Virginia Power’s grid. Estimated maximum load for this system is 1,514 KW. The 277/480 V system provides power to many of the buildings mechanical and fire suppression systems. Use of transformers also allows the voltage to step down for use in common area lighting and electrical systems. The system is distributed through two switchboards with the first being the initial connection to service. The first switchboard provides power to lower level systems such as the lobby and 2nd floor lighting/receptacles (via 150KVa transformer), 1st floor mechanical units, emergency systems, and the second switchboard located on the roof level. Estimated maximum load for this system on the initial switchboard is 1,831 KW and 1,294 KW on the second switchboard. Stand-by power is available through a 450 KW, diesel generator located on the roof in the machine room.
Lighting
The predominant lighting type for the apartment units is incandescent. The public areas, such as corridors and the lobby, tend to use more fluorescent and high end, designer fixtures, when compared to the simple incandescent fixtures used in the apartments. In the apartments the entry areas use 50W, PAR 30 bulbs in a recessed fixture, as do the shower and tub areas. A 75W, A19 single bulb, pendant fixture is located above the kitchen island with 50W, MR-16 track lighting used around the kitchen and dining areas. The bedrooms and bathrooms receive 40W and 60W, A19 bulbs in combinations varying from 2 to 3 bulb fixtures and are surface or wall mounted. The closets and laundry rooms receive 7W, compact fluorescents. Public spaces primarily use 25W or 32W, T8, 3000K, dual bulb, fluorescent fixtures running on 265 volts.
Mechanical
All of the major required equipment for the mechanical system is located in one of three rooms on the penthouse level. Individual control for each residential unit is achieved using water source heat pumps located in each apartment. The fresh air is provided via four roof top units supplying a total of 22,000 cfm with an EER of 9.8 and a total capacity of 417 mbh per unit using a gas connection. These RTU’s also provide supply air to the public spaces, such as corridors and the lobby. A fifth, packaged RTU, is also located on the penthouse roof to supply conditioned air to the rooftop gym space. This RTU uses electric heat and provides 2000 cfm. The water source heat pumps vary in size from 1 to 5 nominal tons, have EER’s between 11.9 and 14, and use R410A, a non ozone depleting refrigerant. Also, for controls the individual units utilize Energy Star compliant programmable thermostats.
The mechanical system uses two plate and frame heat exchangers to exchange heat from the heat pumps to one of two 400 ton, cross flow type cooling towers located on the west side of the penthouse. Incoming water from the cooling tower is at 85oF, flows at 1200 gpm, and returns to the cooling tower at 95oF. On the heat pump side, the entering water temperature is 100oF, flowing at 1320 gpm, and returns to the heat pumps at 90oF. Hot water for the system is provided via four, natural gas, condensing fire-tube boilers also located in the penthouse.
Plumbing is divided into two zones, high and low, for supply to the apartment units. The system uses the boilers and three heat exchangers to produce hot water that is then passed through an electronic mixing valve to achieve the proper temperature. The 140oF hot water is stored in two 500 gallon tanks with two 80 gallon expansions tanks, all located on the 20th floor.
Structure
Given the nature of the Crystal Plaza II project, the structure can be broken down into two distinct sections. The existing structure, from levels 1 to 12, is a 10” deep, rebar reinforced, two way, flat slab with drop panels around corner columns at critical points. The columns from ground level to the second floor slab are 20” diameter, circular columns, while all other columns are square and 18”x18” for exterior or 20”x20” for interior. As part of the renovation, carbon fiber reinforcing is used to assist the existing structure in the bearing capacity of the new structure and is applied to the columns under critical load. Steel W shapes are used around slab cuts for the larger openings in the existing slab and include the use of W8x15, W8x21, W8x35, W10x45, W12x45, and W12x58. A shear wall is also part of the renovated structural system up to the 12th floor. Given the building’s new height, a 10” thick shear wall with #9 and #5 rebar spaced has been constructed.
The new structure is a 6”, post tensioned, 5000 psi, flat plate slab. It has a design live load of 50 psf, including 10 psf for partitions, and uses 8000 psi concrete “puddling” over designated columns. Columns are also reinforced with shear heads in all directions while other reinforcing in the slab and around openings is #4 rebar. The post tension cables vary in stressing from 51 kips to 270 kips depending on location and direction. The penthouse slab is an 8” thick, 5000 psi slab reinforced with #5 rebar. The penthouse roof is a 12” thick, 5000 psi slab reinforced with #6 rebar. The design live load of the roof is 60 psf, including the 30 psf snow load, and the penthouse floor has an increased design live load of 150 psf at mechanical equipment areas. Also on the penthouse floor slab, the structure requires specially designed beams ranging from 12”x58” to a post tensioned 36”x48” beam for support of the swimming pool. Columns for the new structure are identical in size to the existing columns below, however, use of sloped columns are employed at the corner columns on floors 12 and 13 to adjust to the new floor layout and structure.
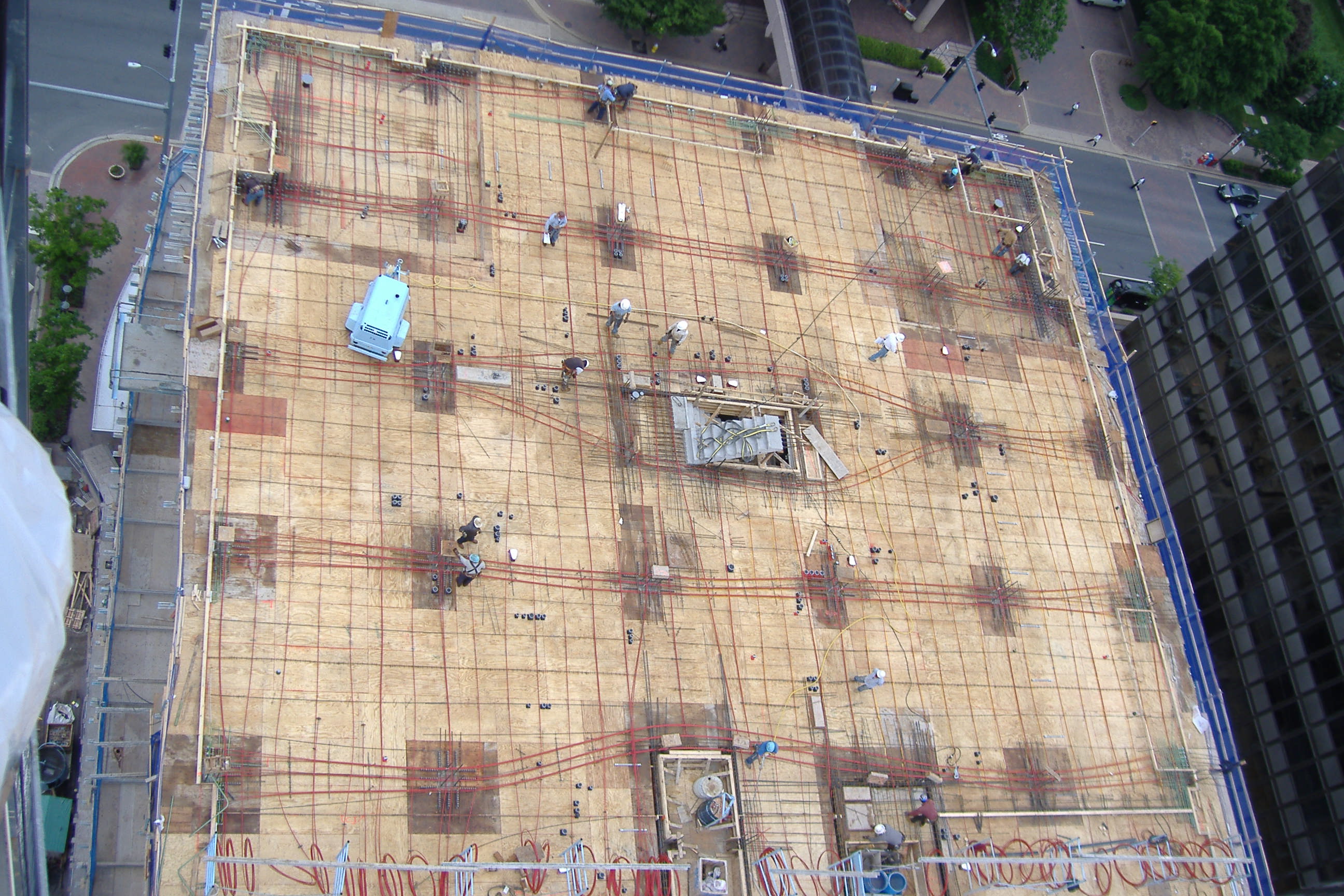
Additional Engineering Support Systems
Fire Protection
The fire protection system for Crystal Plaza II is a design build system with only the pump room in the lower garage level shown on the construction documents. The system utilizes both wet and dry systems. In all locations that are temperature controlled, the wet system is used, while unconditioned areas, such as the garage, are dry to avoid the pipes freezing in low temperature conditions. The wet pipes that travel through the unconditioned areas are insulated, heat traced, or both depending on the location. The standpipe risers are all 6” in diameter with 2” branches to the hose valves located in the two primary stair towers. The sprinkler heads branch off at each floor and include tamper switches before the first sprinkler head. The dry system uses an oil-less air compressor to fill the lines for levels G1 and G2. On the exterior of the building is a 4” fire pump test connection and a 4” Siamese connection for the local fire department.
Transportation
The vertical transportation system selected for Crystal Plaza II is an innovative system that requires no additional machine room for the elevator equipment. Use of Otis’s Gen II elevator system provides elevators that are 50% more efficient and travel at 400 fpm. The travel at Crystal Plaza II is 211’-8”, with an overhead hoist way machine location, and is lifted by steel reinforced belts rather than steel cables. Each car has a capacity of 3000 pounds and is powered by 480 V, 3 phase service. Although no machine room is required, the designed elevator machine room will be used to house the elevator controllers for the system.
Telecom, Security, Other Systems
The owner has elected to provide the telecom and security systems used on the project. They have selected Verizon as the telecom contractor, and Kastle Systems as its security contractor. Verizon will provide there FiOS cable system with high speed internet and Kastle will provide cameras and card readers for the entrances that will be monitored at the leasing office and the concierge desk in the lobby. A final system is the centralized trash chute located adjacent to the single elevator bay for collection.
|